Mastering Process Improvement: Key Strategies for Delaware Manufacturers
Understanding the Importance of Process Improvement
In the competitive landscape of manufacturing, particularly within Delaware, mastering process improvement is crucial for success. Manufacturers are constantly seeking ways to streamline operations, reduce costs, and enhance product quality. Process improvement is not just about tweaking a few steps; it involves a comprehensive approach to optimizing every facet of production.
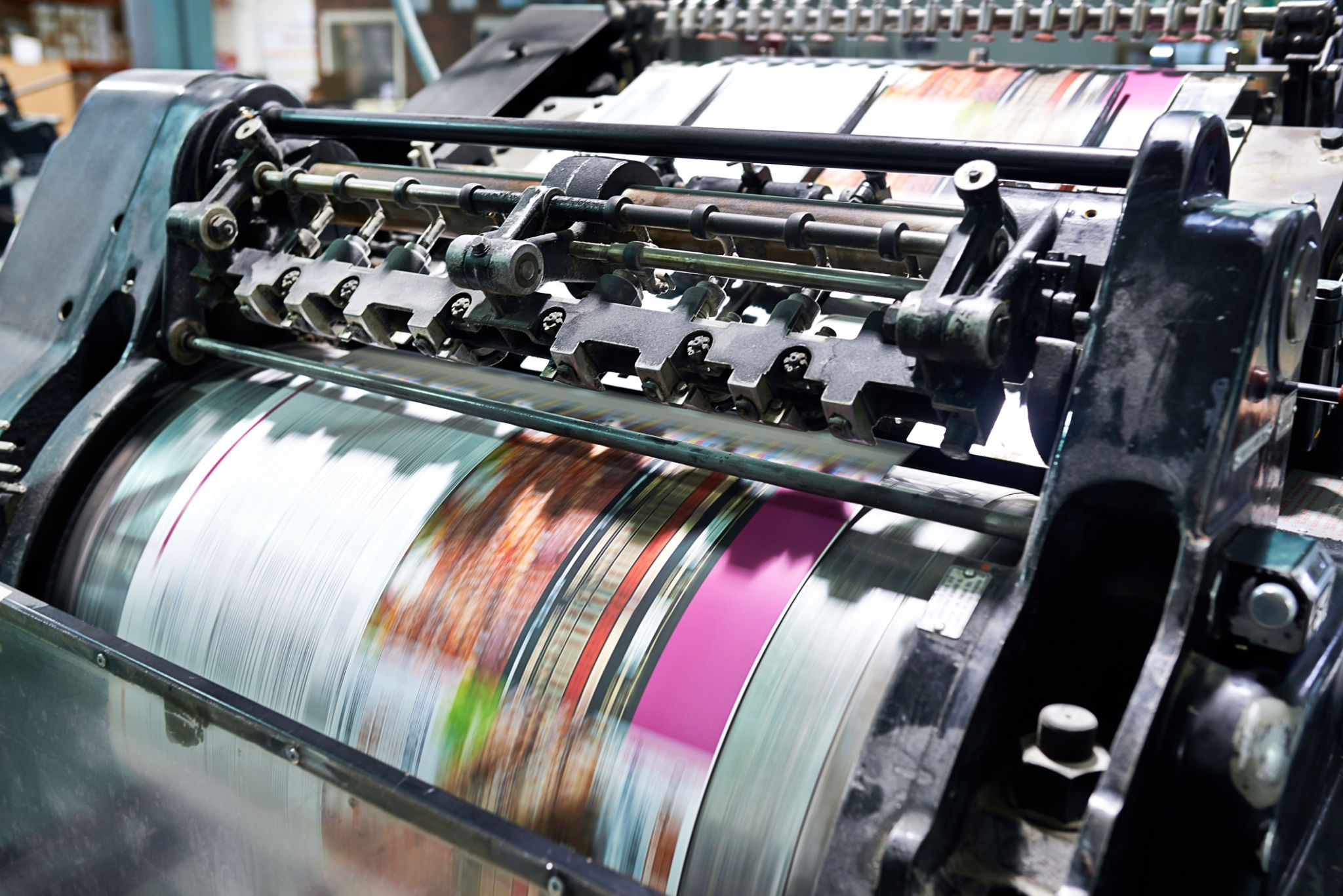
Effective process improvement can lead to increased efficiency and productivity. By identifying bottlenecks and eliminating waste, manufacturers can produce more with the same resources. This not only saves time but also reduces expenses, thereby boosting the bottom line.
Implementing Lean Manufacturing Techniques
Lean manufacturing is a widely recognized strategy for process improvement. It focuses on minimizing waste while maximizing value to the customer. Delaware manufacturers can benefit significantly from adopting lean principles, such as Just-In-Time production and continuous improvement (Kaizen).
Implementing lean techniques requires a cultural shift within the organization. Employees at all levels need to be engaged and committed to identifying inefficiencies and suggesting improvements. It’s about creating a mindset where everyone is constantly looking for ways to do things better.
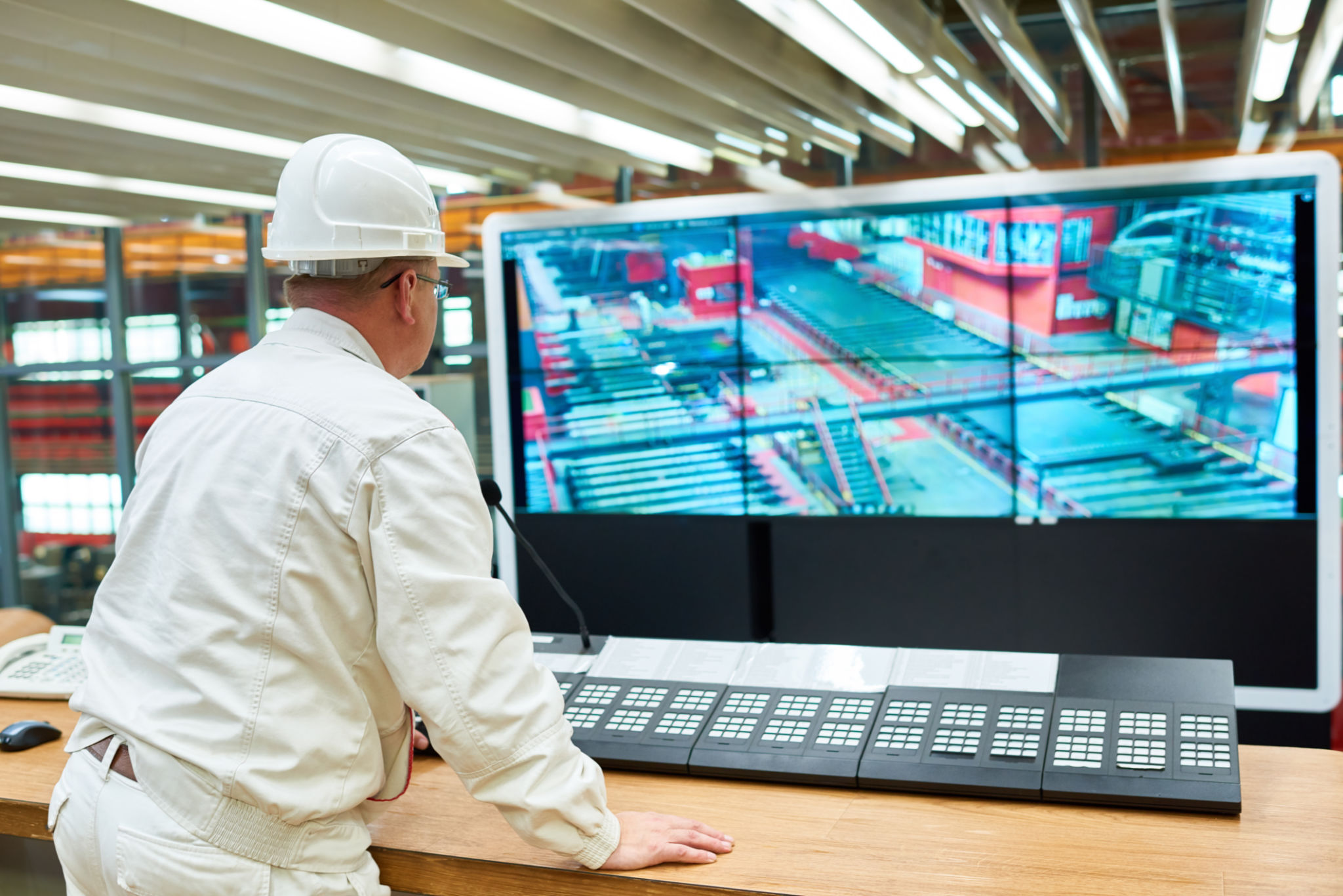
Steps to Implement Lean Manufacturing
- Assess current processes to identify areas of waste.
- Engage employees in brainstorming sessions for improvement ideas.
- Establish clear goals and metrics to measure progress.
- Continuously review and refine processes based on feedback and results.
Leveraging Technology for Enhanced Efficiency
Technology plays a pivotal role in process improvement. Advanced manufacturing technologies such as automation, IoT, and AI can significantly enhance operational efficiency. For Delaware manufacturers, integrating these technologies into their processes can lead to faster production times and reduced error rates.
Automation can handle repetitive tasks, freeing up human resources for more complex problem-solving activities. IoT devices can provide real-time data insights, allowing managers to make informed decisions that optimize production schedules and maintenance processes.
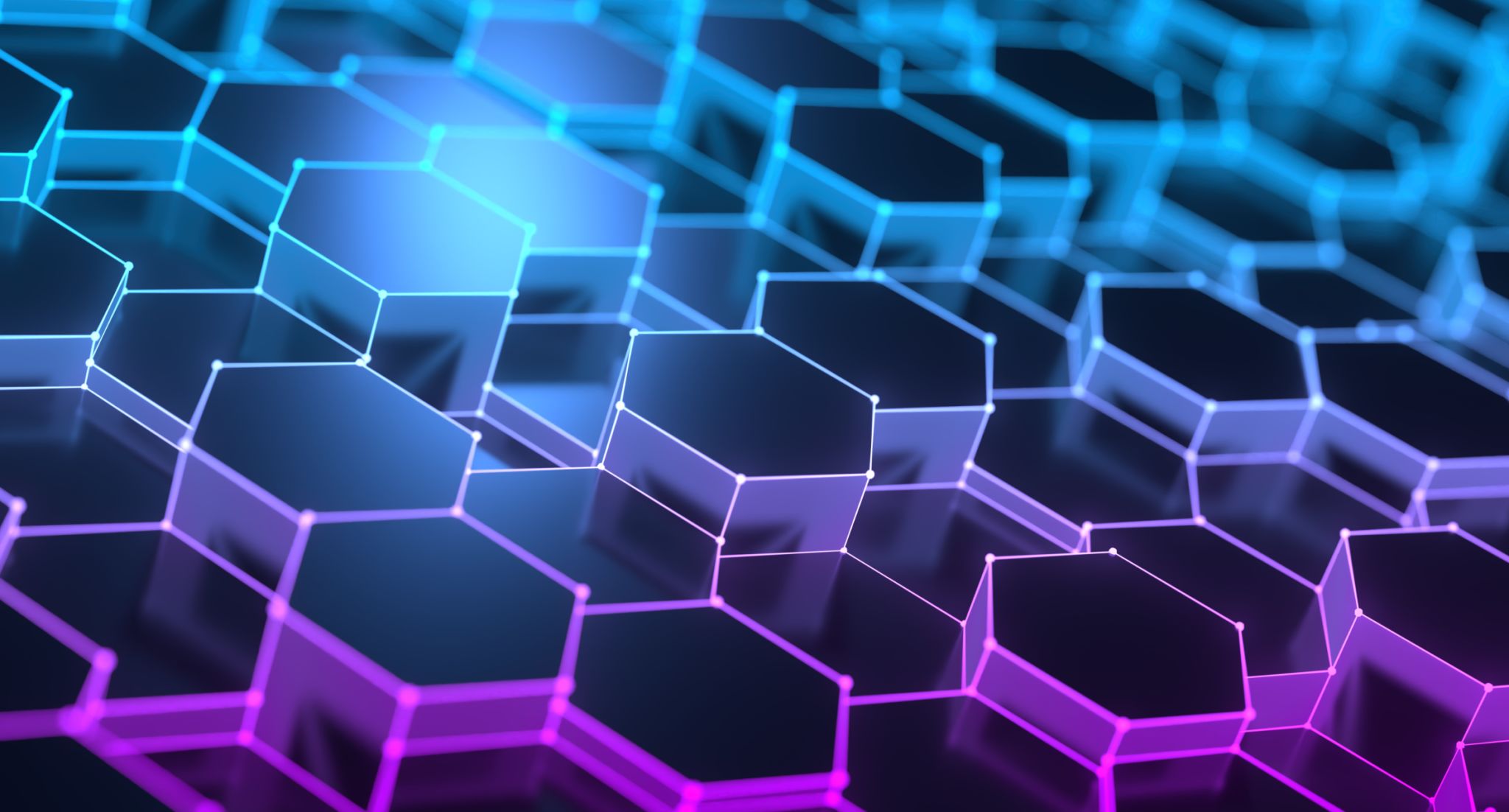
Choosing the Right Technology
Selecting the appropriate technology requires careful consideration of specific business needs and goals. Manufacturers should start by evaluating their current capabilities and identifying gaps where technology could provide solutions. Partnering with technology providers can also offer valuable expertise and support during implementation.
Continuous Training and Development
A successful process improvement strategy involves continuous training and development of the workforce. Employees need to be equipped with the skills and knowledge necessary to adapt to new processes and technologies. Regular training sessions can help maintain high levels of performance and productivity.
Moreover, fostering a culture of continuous learning encourages innovation and keeps the workforce engaged. This empowers employees to contribute actively to process improvement initiatives, driving the company towards achieving its strategic objectives.
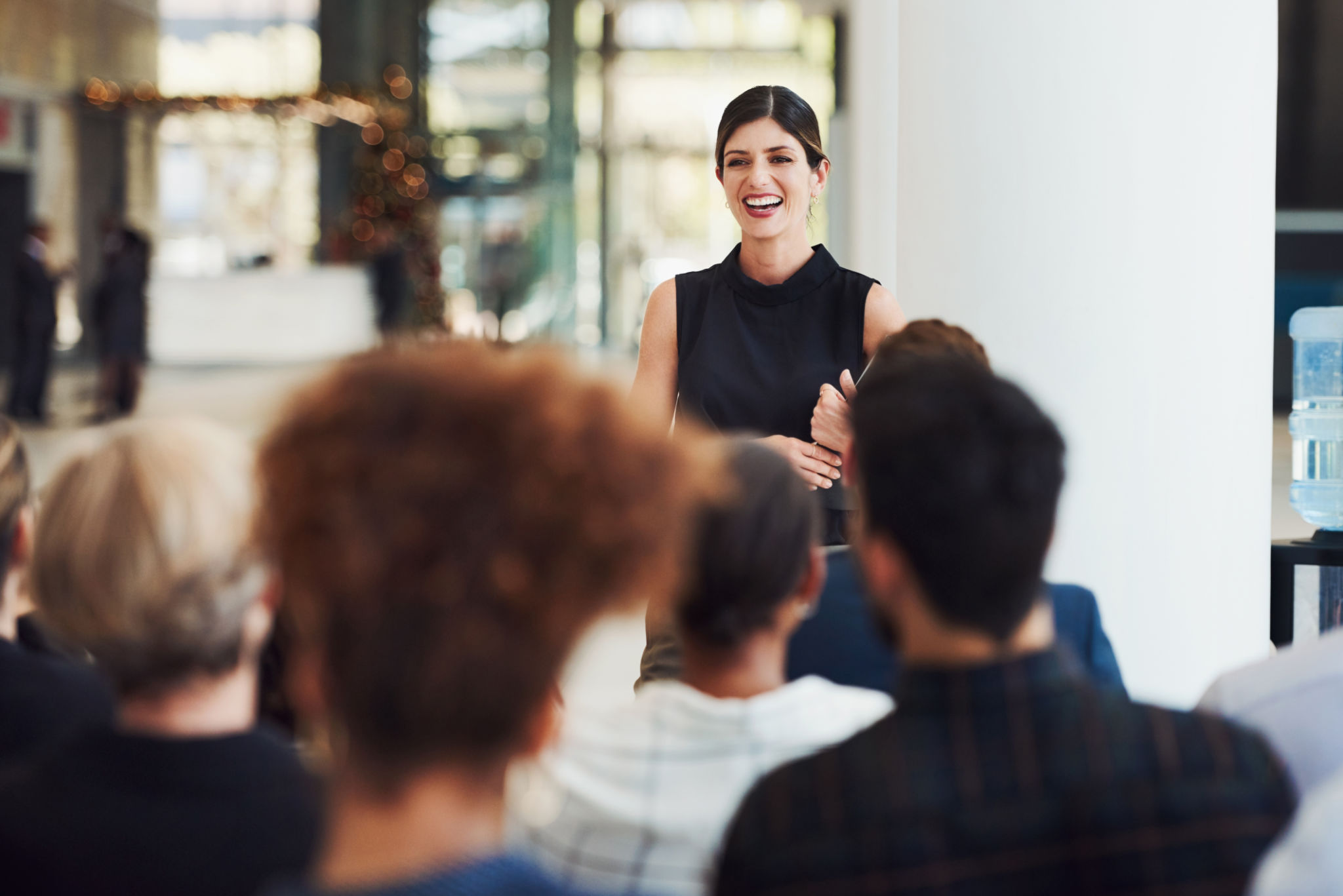
The Role of Leadership in Process Improvement
Leadership plays a critical role in the success of process improvement initiatives. Effective leaders inspire their teams, set clear visions, and allocate resources efficiently. By prioritizing process improvement, leaders can ensure sustainable growth and long-term competitiveness in the manufacturing sector.
In conclusion, mastering process improvement is essential for Delaware manufacturers aiming to thrive in today’s dynamic market environment. By embracing lean manufacturing, leveraging technology, investing in employee development, and demonstrating strong leadership, manufacturers can optimize their operations, reduce costs, and enhance product quality.